Circuito impreso de doble faz: Guía esencial para principiantes
Los circuitos impresos de doble faz son una tecnología fundamental en la industria electrónica actual. Estos circuitos, también conocidos como PCB de doble cara, cuentan con trazas de cobre en ambos lados de la placa, lo que permite una mayor densidad de componentes y una mejor distribución de las conexiones eléctricas. En esta era de dispositivos electrónicos cada vez más compactos y de alto rendimiento, la capacidad de aprovechar al máximo el espacio disponible y mejorar la funcionalidad de los circuitos es esencial.
El diseño y fabricación de circuitos impresos de doble faz puede ser un proceso complejo, ya que implica múltiples etapas, desde la creación del esquema y el diseño de la placa, hasta la producción y ensamblaje de los componentes. Una de las principales ventajas de esta tecnología es la posibilidad de reducir la distancia entre los componentes y las conexiones, lo que a su vez minimiza la interferencia entre señales y mejora la eficiencia energética del dispositivo.
El uso de circuitos impresos de doble faz no se limita a una sola industria; se encuentran en una amplia gama de aplicaciones, desde la electrónica de consumo hasta la automotriz, pasando por sistemas de comunicaciones y dispositivos médicos. Con la evolución constante de la tecnología y la creciente demanda de soluciones electrónicas más avanzadas, es probable que los circuitos impresos de doble faz sigan siendo una herramienta clave en el desarrollo de dispositivos y sistemas electrónicos en un futuro próximo.
Doble Faz: Características y Ventajas
Características
Los Circuitos Impresos de Doble Faz (también conocidos como PCB de doble cara) consisten en dos capas de cobre en las cuales se montan los componentes electrónicos. Estas dos capas están separadas por un material dieléctrico, lo que permite una mayor densidad de componentes y conexiones. Algunas características clave de los PCB de doble faz incluyen:
- Mayor densidad de interconexiones: Esta característica permite tener más componentes en un área más pequeña, lo que se traduce en dispositivos compactos y ligeros.
- Disposición de componentes en ambas caras: Los componentes pueden montarse en ambas caras del PCB, lo que permite una mayor densidad y versatilidad en el diseño del circuito.
Ventajas
Los circuitos impresos de doble faz ofrecen numerosas ventajas en comparación con los PCB de una sola cara. Entre ellas se encuentran:
- Más espacio disponible: El uso de ambas caras del PCB para el montaje de componentes permite aprovechar de manera más eficiente el espacio disponible.
- Mayor capacidad de disipación de calor: La dispersión del calor es más eficiente en los circuitos impresos de doble faz ya que cuentan con una mayor superficie de cobre.
- Coste competitivo: Aunque son un poco más costosos que los PCB de una sola cara, ofrecen una mayor versatilidad y eficiencia a un precio razonable.
- Diseños más complejos: Gracias a la mayor densidad de interconexiones, los PCB de doble faz pueden albergar diseños de circuitos más complejos y avanzados.
- Mejora en el rendimiento del circuito: Al reducir la necesidad de conexiones indirectas entre componentes, los PCB de doble faz pueden mejorar el rendimiento del circuito al reducir la resistencia y la cantidad de ruido que se introduce en el sistema.
En resumen, los circuitos impresos de doble faz ofrecen una solución efectiva y versátil para el diseño y montaje de circuitos electrónicos.
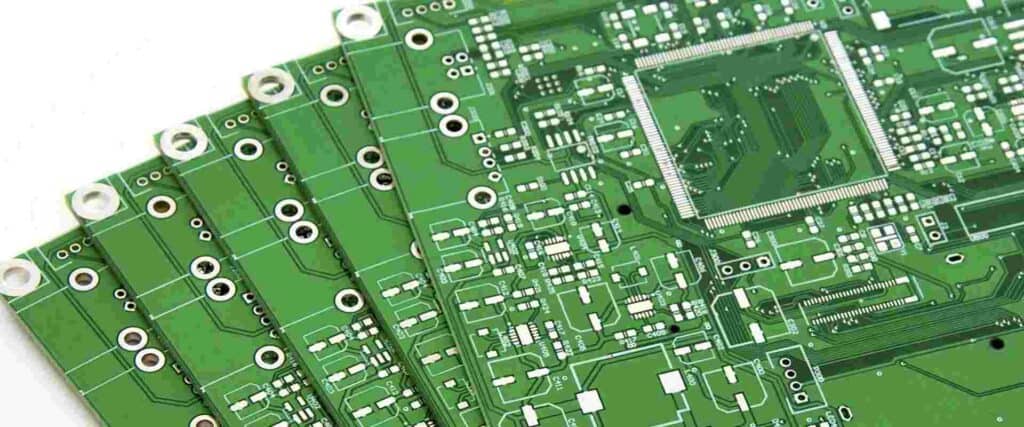
Materiales y Componentes
Materiales Base
Para la fabricación de circuitos impresos de doble faz, se utilizan dos tipos de materiales base principales:
-
FR4: Es el material más utilizado debido a su durabilidad, estabilidad térmica y resistencia al fuego. Está compuesto por una lámina de fibra de vidrio impregnada con resina epoxi.
-
CEM: Este material es similar al FR4, pero está compuesto por láminas técnicas celulosas en su núcleo y láminas de fibra de vidrio en las superficies exteriores. Es más económico, pero posee menor estabilidad térmica.
Es importante elegir el material base adecuado según las necesidades del proyecto.
Componentes Electrónicos
En un circuito impreso de doble faz, se pueden encontrar diversos componentes electrónicos, como resistencias, condensadores, inductores, diodos y transistores, además de circuitos integrados y conectores. Éstos se clasifican según su función y características eléctricas:
- Resistencias: Se utilizan para limitar el flujo de corriente y reducir voltajes en un circuito.
- Valores típicos:
100Ω
,1kΩ
,10kΩ
- Valores típicos:
- Condensadores: Se emplean para el almacenamiento temporal de energía y la filtración de señales.
- Valores típicos:
100nF
,1μF
,10μF
- Valores típicos:
- Inductores: Sirven para almacenar energía en forma de campo magnético y filtrar señales de alta frecuencia.
- Valores típicos:
10μH
,100μH
,1mH
- Valores típicos:
Componente | Función | Valores típicos |
---|---|---|
Resistencia | Limitar corriente | 100Ω, 1kΩ, 10kΩ |
Condensador | Almacenamiento de energía | 100nF, 1μF, 10μF |
Inductor | Filtrado de señales | 10μH, 100μH, 1mH |
Seleccionar y ubicar los componentes adecuados en el circuito es fundamental para el diseño y funcionamiento óptimo del mismo.

Proceso de Fabricación
Diseño y Esquemático
El primer paso en la fabricación de un circuito impreso de doble faz es el diseño del esquemático. Se utiliza software de diseño asistido por computadora (CAD) para crear el diagrama esquemático del circuito. Este diagrama muestra los componentes del circuito y cómo se conectan entre sí. Una vez completado el esquemático, se genera el diseño de la placa, que muestra la ubicación de los componentes y las pistas de cobre que los conectan.
Transferencia de Imágenes y Cobre
El siguiente paso en la fabricación es la transferencia de imágenes y cobre. Primero, se coloca una lámina de cobre sobre la placa, que luego se cubre con una capa de material fotosensible. Se utiliza una película para transferir el diseño de la placa al material fotosensible. Luego, se expone la placa a la luz ultravioleta, que endurece el material fotosensible en las áreas expuestas. Finalmente, se eliminan las áreas no expuestas, dejando el diseño de cobre en la placa.
Perforación y Montaje
Una vez completada la transferencia de imágenes, se perforan agujeros en la placa para los componentes electrónicos. Esto se hace utilizando una máquina de perforación de control numérico computarizado (CNC) para garantizar la precisión y consistencia de los agujeros. Después de que se han perforado los agujeros, los componentes electrónicos se montan en la placa utilizando un proceso llamado inserción de componentes. Los componentes se colocan en los agujeros y se aseguran con una máquina de soldar por ola.
Soldadura y Acabado
El último paso en la fabricación de un circuito impreso de doble faz es la soldadura y el acabado. Los componentes se sueldan a la placa utilizando una máquina de soldar por ola. La máquina de soldar por ola aplica una capa de soldadura al cobre, lo que asegura los componentes a la placa y permite la conexión eléctrica. Finalmente, la placa se limpia para eliminar cualquier residuo y se aplica una capa de acabado para proteger el cobre y garantizar la calidad y durabilidad del circuito impreso.
Aplicaciones y Usos Comunes
Los circuitos impresos de doble faz tienen aplicaciones en diversos campos de la electrónica y la tecnología debido a su capacidad para albergar una mayor cantidad de componentes y conexiones. A continuación, se mencionan algunas de sus aplicaciones y usos comunes:
Electrónica de consumo
Los circuitos impresos de doble faz son comunes en la fabricación de dispositivos electrónicos de consumo, como televisores, computadoras, teléfonos móviles y electrodomésticos. Permiten un mejor rendimiento y mayor densidad de componentes en estos dispositivos.
Industria automotriz
En la industria automotriz, estos circuitos se utilizan en sistemas de control de motor, GPS, sistemas de frenado antibloqueo (ABS) y sistemas de seguridad. Ayudan a mejorar la eficiencia y confiabilidad de los vehículos.
Sistemas de comunicaciones
La tecnología de doble faz también es esencial en sistemas de comunicación, incluidos los equipos de radio, redes de telefonía y sistemas de fibra óptica. Facilitan la transferencia rápida y confiable de datos entre dispositivos.
Energías renovables
Los circuitos impresos de doble faz tienen aplicaciones en la industria de energías renovables, como los sistemas fotovoltaicos y los sistemas de almacenamiento de energía. Contribuyen a la eficiencia y al rendimiento de estos sistemas.
En resumen, los circuitos impresos de doble faz son esenciales en una amplia variedad de aplicaciones y usos comunes en diversas industrias. Su capacidad para albergar una mayor cantidad de componentes y conexiones los hace una parte integral de la tecnología moderna.

Mantenimiento y Solución de Problemas
Mantenimiento Preventivo
El mantenimiento preventivo es fundamental para garantizar un buen funcionamiento y prolongar la vida útil de un circuito impreso de doble faz. Algunas de las acciones a considerar son:
- Limpiar periódicamente el circuito con un paño suave y sin pelusas, utilizando alcohol isopropílico o una solución específica para la limpieza de circuitos
- Inspeccionar el circuito en busca de grietas o signos de fatiga, especialmente en las áreas de mayor carga
- Verificar las soldaduras y conexiones, rehacerlas si es necesario
Detección y Solución de Problemas
A continuación, se mencionan algunas cuestiones frecuentes y sus posibles soluciones:
-
Cortocircuito: Detectar el cortocircuito utilizando un multímetro en función de continuidad. Ubicar el área afectada y repararla, ya sea eliminando la conexión no deseada o resoldando el segmento.
-
Pistas dañadas: Examinar visualmente el circuito y buscar signos de daño en las pistas, como roturas o abrasiones. Si se encuentra daño en una pista, repararla utilizando una tira de cobre autoadhesiva y retocar con soldadura.
-
Componentes defectuosos: Utilizar un multímetro para medir la resistencia, voltaje y corriente de los componentes en el circuito y comparar con los valores especificados. Reemplazar los componentes defectuosos si es necesario.
Herramientas necesarias
Algunas herramientas útiles para realizar el mantenimiento y solución de problemas en un circuito impreso de doble faz incluyen:
- Multímetro
- Soldador y estaño
- Limpiador de circuitos
- Lupa o microscopio
- Tira de cobre autoadhesiva
Al seguir las recomendaciones brindadas respecto al mantenimiento preventivo y solución de problemas, es posible garantizar un funcionamiento óptimo y prolongar la vida útil de un circuito impreso de doble faz.
Consideraciones Ambientales
Los circuitos impresos de doble faz tienen un impacto en el medio ambiente debido a la fabricación, uso y desecho, es importante tomar en cuenta ciertos factores en cada etapa.
Fabricación
- Materiales: Para reducir la huella ambiental, se pueden utilizar materiales reciclados en la producción de circuitos impresos de doble faz. Esto incluye metales y plásticos reciclados.
- Proceso de producción: El uso de tecnologías y procesos amigables con el ambiente, como técnicas de mecanizado, puede reducir el consumo de energía y la generación de residuos.
Uso
- Eficiencia energética: Los circuitos impresos de doble faz deben ser diseñados de manera que maximicen la eficiencia energética. Esto incluye la utilización de componentes de bajo consumo y optimización del diseño del circuito para minimizar pérdidas de energía.
- Emisiones de Gases de Efecto Invernadero (GEI): El diseño debe tener en cuenta las posibles emisiones de gases GEI, especialmente aquellos que son perjudiciales para la capa de ozono, como CFCs.
Desecho
- Reciclaje de componentes y materiales: Los circuitos impresos de doble faz deben ser reciclables al final de su vida útil. Esto implica utilizar materiales y componentes fácilmente separables y reciclables.
- Tratamiento de residuos: Es importante gestionar adecuadamente los residuos generados durante el desecho de los circuitos impresos, para evitar la liberación de sustancias tóxicas al medio ambiente. Esto incluye el tratamiento de productos químicos y la eliminación adecuada de materiales no reciclables.
Al considerar estos factores, es posible contribuir a la reducción de los impactos ambientales asociados con los circuitos impresos de doble faz y promover prácticas más sostenibles.
Conclusión
El circuito impreso de doble faz es una herramienta esencial en la electrónica moderna. Su capacidad para alojar componentes electrónicos en ambas caras permite una mayor densidad y complejidad en el diseño de los dispositivos electrónicos.
Las ventajas de estos circuitos incluyen:
- Ahorro de espacio
- Menor longitud de las rutas de conexión
- Mayor capacidad para implementar circuitos más complejos
La fabricación de circuitos impresos de doble faz requiere habilidad y precisión, pero su utilización se traduce en una mejora general en la funcionalidad y la eficiencia de los dispositivos.
En cuanto a la fabricación, es válido plantear que:
- Los avances tecnológicos han facilitado la creación de circuitos de doble faz.
- La automatización en el proceso de producción permite menor margen de error.
Por último, es importante señalar la relevancia de considerar al medio ambiente en el proceso de fabricación y eventual descarte de estos circuitos. La investigación y desarrollo de materiales ecológicos y sistemas reciclables contribuye a promover la sostenibilidad en la industria electrónica.