El proceso de fabricación de circuitos impresos (PCB) es un tema fascinante y crucial en la industria electrónica actual. Los circuitos impresos son la base de la mayoría de los dispositivos electrónicos que utilizamos a diario, desde teléfonos móviles y computadoras hasta sistemas de control para automóviles y electrodomésticos. En este artículo, exploraremos los pasos clave y las técnicas involucradas en la producción de PCB de alta calidad.
El proceso de fabricación de PCB generalmente comienza con el diseño del circuito en un programa de diseño electrónico (EDA). Una vez que se ha creado el diseño, se seleccionan los materiales adecuados, como el tipo de laminado, el espesor del cobre y otros componentes esenciales, para cumplir con las especificaciones técnicas y requisitos específicos del proyecto. Luego, se lleva a cabo la producción del PCB a través de múltiples etapas, que incluyen la impresión de circuitos, el grabado, la perforación, el montaje de componentes y la soldadura.
Cabe destacar que hay diferentes tipos de tecnologías de PCB como los de capa única, doble cara y multicapa. Cada uno de estos requiere un enfoque distinto en la fabricación para garantizar la calidad y la eficiencia. En resumen, el proceso de fabricación de circuitos impresos es un conjunto de prácticas sofisticadas que garantizan la producción de componentes electrónicos confiables y de alto rendimiento. Esta exploración en profundidad nos permitirá comprender mejor la importancia de cada paso en la producción de PCB y su impacto en la fabricación de productos electrónicos en general.
Materiales Utilizados en Circuitos Impresos
Lámina de Cobre
La lámina de cobre es el material conductor principal utilizado en la fabricación de circuitos impresos. Se adhiere a la superficie del sustrato aislante para formar las pistas y conexiones eléctricas. El grosor de la lámina de cobre puede variar dependiendo de las necesidades específicas del circuito impreso.
Substratos Aislantes
Los sustratos aislantes son la base sobre la cual se montan los componentes y se trazan las pistas conductoras en un circuito impreso. Los materiales comunes utilizados en sustratos aislantes incluyen:
- Fibra de vidrio: Es un material rígido y resistente que soporta altas temperaturas. Es la opción más común en circuitos impresos.
- Papel fenólico: Es un material económico utilizado en aplicaciones de baja potencia y baja frecuencia.
- Polímeros (como poliimida): Son utilizados en aplicaciones de alta temperatura y alta frecuencia, debido a sus propiedades aislantes y estabilidad térmica.
Materiales Dieléctricos
Los materiales dieléctricos son utilizados en circuitos impresos para separar y aislar capas conductoras adyacentes. Estos materiales son especialmente importantes en circuitos de múltiples capas donde la interferencia electromagnética y la capacitancia parásita deben minimizarse. Algunos ejemplos de materiales dieléctricos comunes incluyen:
- FR-4: Es el material dieléctrico más común en la industria de circuitos impresos, hecho de fibra de vidrio y resina epoxi.
- Poliimida: Utilizado en aplicaciones de alta temperatura y alta frecuencia. Resistente a la mayoría de productos químicos, su densidad y flexibilidad permiten su uso en una variedad de aplicaciones.
- PTFE (Politetrafluoroetileno): Conocido por su baja constante dieléctrica, es ideal para aplicaciones de alta frecuencia como antenas y sistemas de radar.
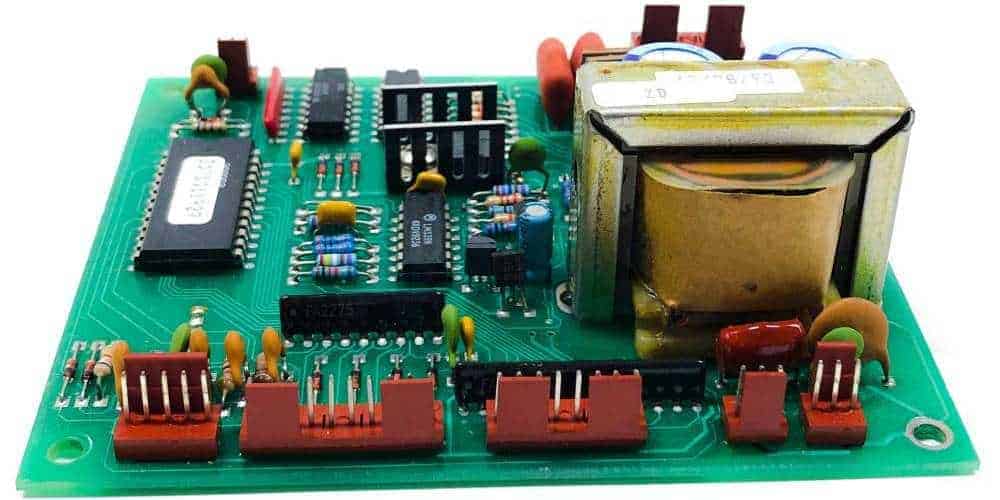
Diseño del Circuito Impreso
Diseño Esquemático
El diseño esquemático es la primera etapa en la creación de un circuito impreso. Aquí, se realiza la representación gráfica de los componentes electrónicos y sus interconexiones. Se utiliza software especializado para este paso, como Eagle o KiCad.
- Selección de componentes: Se eligen los dispositivos electrónicos necesarios para el funcionamiento del circuito.
- Conexión de componentes: Se establecen las conexiones entre los componentes, de acuerdo con el esquema eléctrico del circuito.
- Comprobación del diseño: Se analiza el circuito esquemático para asegurarse de que cumple con los requerimientos eléctricos y funcionales.
Diseño del Trazado
Una vez completado el diseño esquemático, se procede al diseño del trazado o enrutamiento de las pistas del circuito impreso. Este proceso suele realizarse también con software especializado, como Altium o Cadence.
- Diseño de la placa: Se crea un archivo con las dimensiones y forma de la placa de circuito impreso.
- Posicionamiento de componentes: Se ubican los componentes en el diseño, siguiendo las mejores prácticas de diseño.
- Evitar la superposición de componentes
- Mantener una distancia mínima entre ellos
- Alinear componentes para optimizar conexiones
- Enrutamiento de pistas: Se trazan las conexiones entre los componentes, utilizando técnicas como enrutamiento manual o autorouting.
- Considerar la impedancia y capacitancia de las pistas
- Minimizar la longitud de las trazas
- Creación de planos de tierra y alimentación: Se definen áreas de cobre para la conexión a tierra y alimentación.
- Verificación: Se realiza una última comprobación del diseño, verificando reglas de diseño y asegurándose de que el circuito cumplirá sus funciones.
Pasos del Proceso de Fabricación
Transferencia del Diseño al Material
En primer lugar, se realiza la transferencia del diseño del circuito impreso al material base, generalmente una placa de cobre laminado sobre sustrato de fibra de vidrio. El diseño se imprime en una lámina y luego se coloca sobre la placa de cobre. A continuación, se utiliza una fuente de luz UV para transferir el diseño a la placa, dejando una imagen resistente al ácido en la superficie del cobre.
Grabado del Cobre
El siguiente paso es el proceso de grabado, donde se sumerge la placa en una solución de ácido para eliminar las áreas de cobre no protegidas por el resistente al ácido. De esta manera, se obtiene el patrón deseado de pistas y pads de cobre. Una vez completo el grabado, se limpia la placa y se retira el resistente al ácido.
Perforación de Orificios
Luego, se procede a perforar los orificios en la placa para permitir la conexión de los diferentes componentes. Estos orificios se realizan con máquinas de precisión, conocidas como taladros CNC, siguiendo las coordenadas del diseño original.
Diámetro del Orificio | Uso Común |
---|---|
0.8 mm | Resistencias y Capacitores |
1.2 mm | Diodos y Transistores |
2.0 mm | Conectores |
Soldadura y Montaje de Componentes
Para finalizar, se lleva a cabo la soldadura y montaje de los componentes electrónicos en la placa de circuito impreso. Existen dos tipos principales de montaje:
- Montaje de superficie (SMD): Se utilizan componentes miniaturizados que se montan directamente sobre las áreas de cobre de la placa.
- Montaje de orificio (PTH): Se emplean componentes con terminales que se insertan en los orificios previamente perforados y luego se sueldan en su sitio.
Una vez soldados los componentes, se realiza una inspección para verificar que no haya fallas en las conexiones y se somete la placa de circuito impreso a pruebas eléctricas para asegurar su correcto funcionamiento.

Técnicas de Manufactura en Escala Industrial
Máquinas de Contacto Directo
El uso de máquinas de contacto directo en la fabricación de circuitos impresos es esencial en la producción en masa. Estas máquinas garantizan una alta precisión y uniformidad en la transferencia de patrones de circuitos en las placas. Algunas máquinas de contacto directo incluyen:
- Máquinas de serigrafía
- Impresoras de almohadilla
- Equipos de chorro de tinta
Estas máquinas aplican los patrones de circuito utilizando presión mecánica y aseguran una cobertura uniforme del material conductor.
Tecnología de Montaje Superficial
La tecnología de montaje superficial (SMT) permite una mayor densidad de componentes en las placas de circuito impreso y reduce el tamaño general de los dispositivos. Este proceso es esencial en la producción en escala industrial de circuitos impresos y utiliza las siguientes técnicas:
- Colocación de componentes: máquinas de colocación automáticas aseguran una alta precisión y velocidad en la instalación de componentes.
- Soldadura por horno de reflujo: los componentes se adhieren a la placa mediante un horno de reflujo que calienta la pasta de soldadura previamente aplicada.
- Inspección y testeo: al realizar inspecciones automáticas, como la inspección óptica automática (AOI), se garantiza un alto grado de calidad en la producción.
Inspección Automática de Soldadura
La inspección automática de soldadura es una parte fundamental en el proceso de fabricación de circuitos impresos en escala industrial. Esta técnica tiene como objetivo garantizar que las conexiones y soldaduras en los componentes sean de alta calidad y libres de defectos. Dos tipos comunes de inspección de soldadura son:
- Inspección óptica automática (AOI): utiliza cámaras y software de análisis de imágenes para detectar defectos en las soldaduras.
- Inspección de rayos X: permite visualizar la calidad de las soldaduras ocultas y de posibles defectos internos en los componentes.
Estas técnicas de inspección ayudan a minimizar el riesgo de defectos y garantizan una producción de alta calidad en la fabricación de circuitos impresos en gran escala.